Real-time packing registration by a dedicated packing line leader.
New Packing Module for Farm Management
Overview
A major hydroponic farm supplier tasked us with creating a brand new module for their existing farm management platform. This module would specifically address the packing and shipping processes for their products, aiming to streamline communication and task allocation between the shipment and packing crews.
As UX designer, information architect, and user researcher, I played a pivotal role in crafting this new module. I spearheaded user understanding through workshops and interviews, then translated those insights into a user-friendly and efficient design solution.
Role
- UX Design
- Visual Design
- Information architecture
- Workshop facilitator
- UX Writing
- Prototyping
- Testing
Date
2023 - 2024
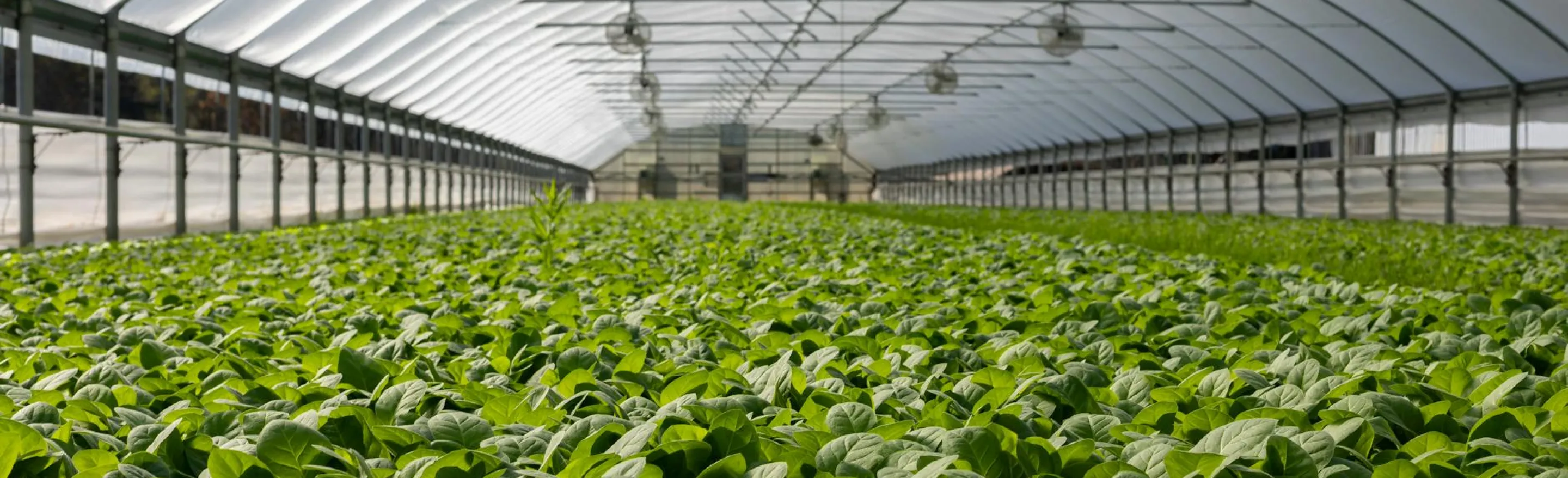
Challenges and Current Landscape
While the farm already had a platform for managing other aspects of their operation, the packing and shipping processes relied heavily on a patchwork of spreadsheets and informal messaging. This led to inefficiencies, communication breakdowns, and a lack of real-time visibility into progress and potential issues.
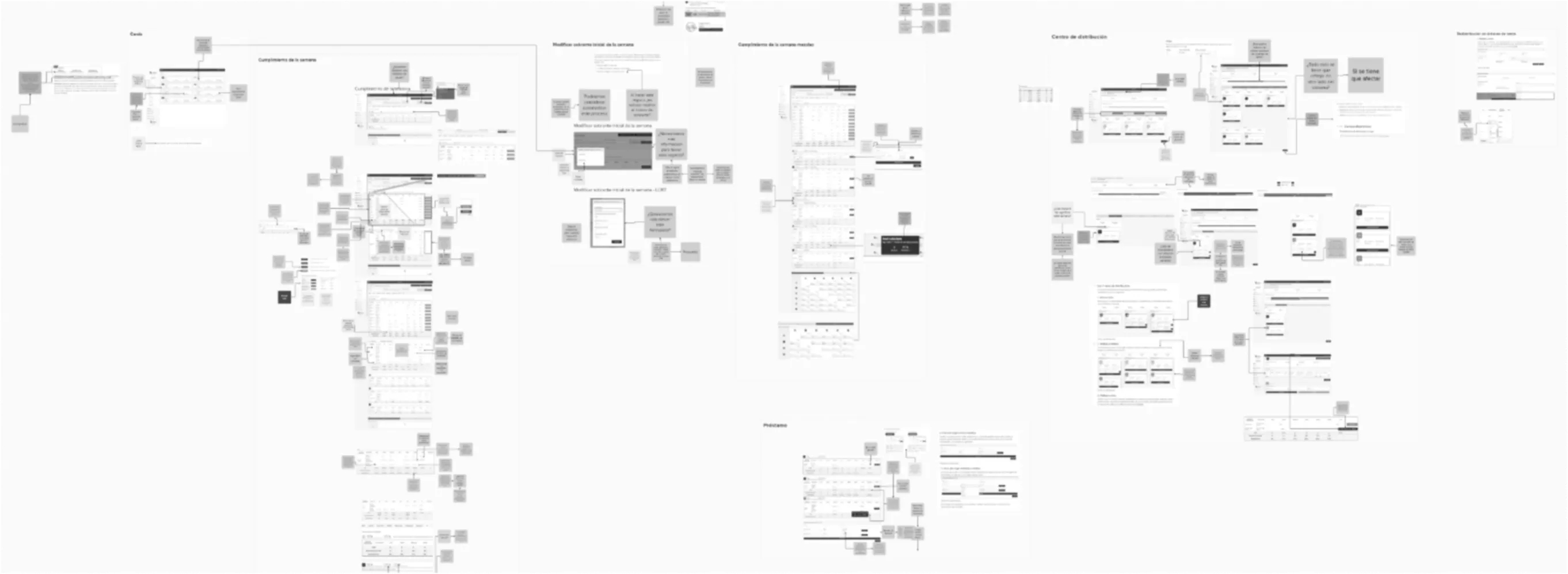
Embracing User-Centered Design
To ensure the new module met the specific needs of the farm's workflow, we prioritized user-centered design principles. This involved conducting workshops and user interviews with key stakeholders, particularly the shipment leader and packing leader, who would be the primary users of the module. Through these sessions, we aimed to gain a deep understanding of their daily tasks, pain points, and desired functionalities.
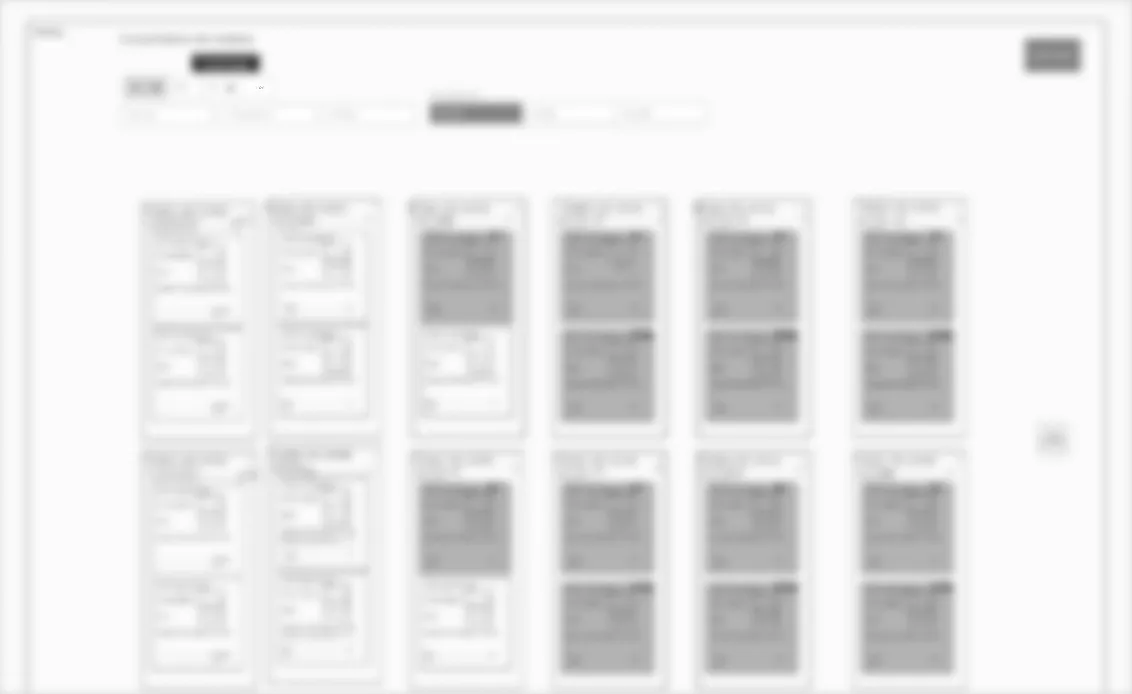
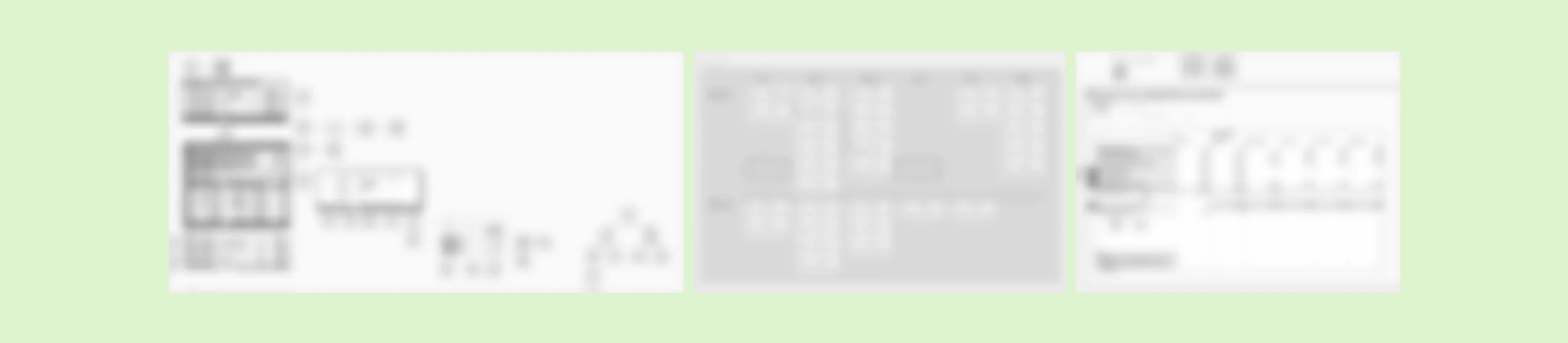
Deep User Understanding
Through workshops and user interviews, we delved into the user workflows, analyzing the vast spreadsheets used to manage tasks. This revealed a complex, real-world process far removed from the initial platform's simplified model. By understanding user pain points and their daily routines, we could redefine the critical tasks performed by the shipment and packing leaders
Shipment Leader
Receive client orders with product details, packaging types, client information, and due dates.
Negotiate adjustments with clients if harvest yields fall short.
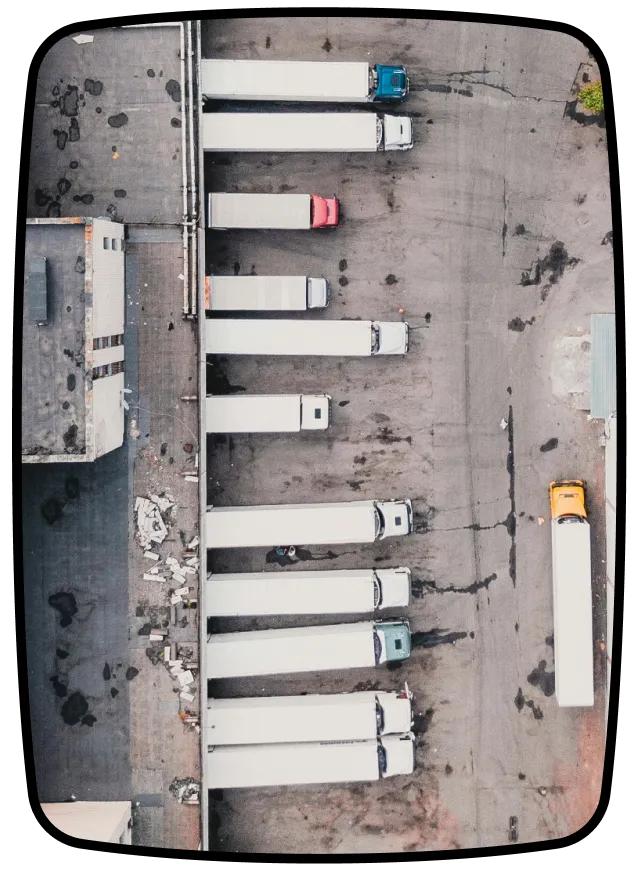
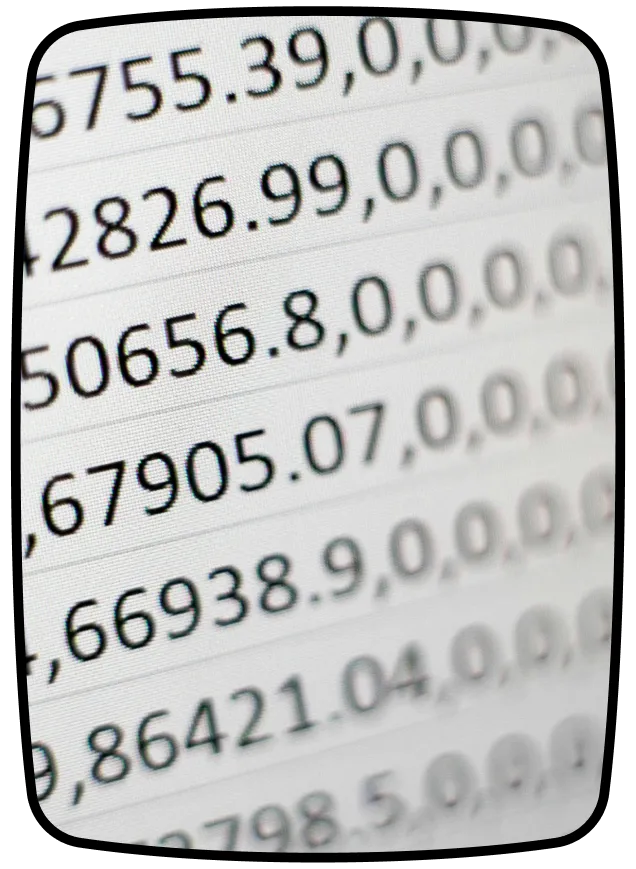
Packing Leader
Assign greenhouses based on anticipated harvest data for ordered products.
Allocate packing locations based on physical constraints.
Split items according to packing schedules for the crew.
Monitor packing progress in real-time, identifying potential delays and missing items.
Communicate with the shipment leader if adjustments are needed.
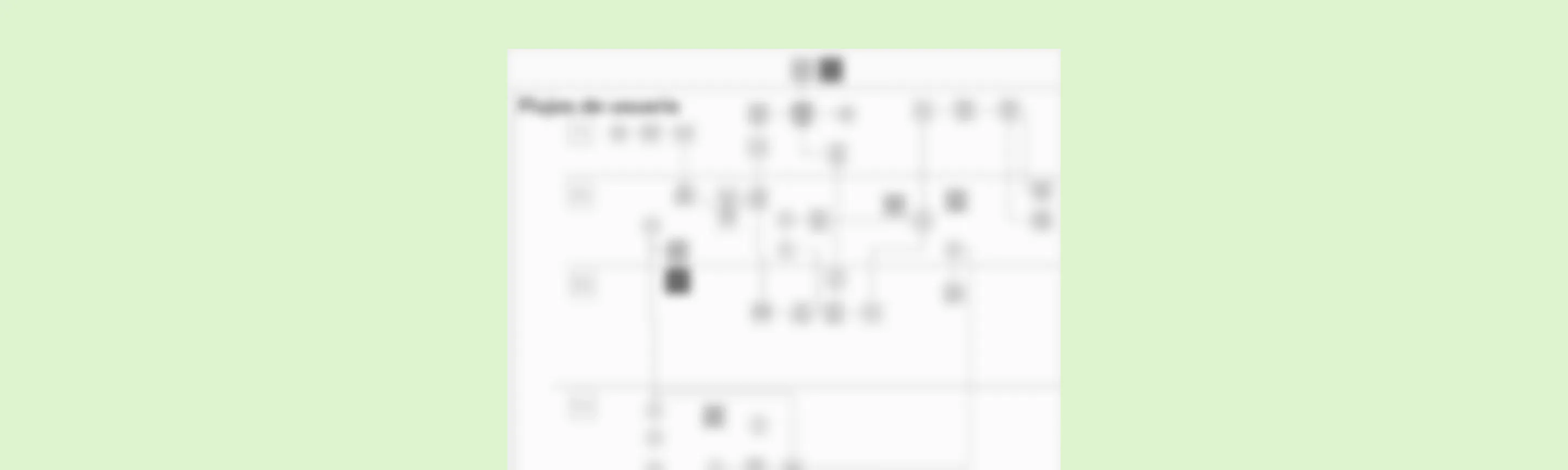
Identifying Gaps and Introducing New Features
This deep dive into user needs also exposed the need for features not present in the initial design, such as:
Past week packing management and potential overpacking identification.
Greenhouse assignment based on requested product availability.
Packing status updates for individual items and entire shipment orders.
Continuous Collaboration and Iteration
Throughout the project, clear communication and close collaboration were essential. We maintained constant communication with the development team, meticulously documenting user needs and functionalities to avoid potential roadblocks during development.
Iterative Design for Optimal Results
We embraced an iterative design process, incorporating user feedback at every stage. We created low-fidelity prototypes to test various features, including:
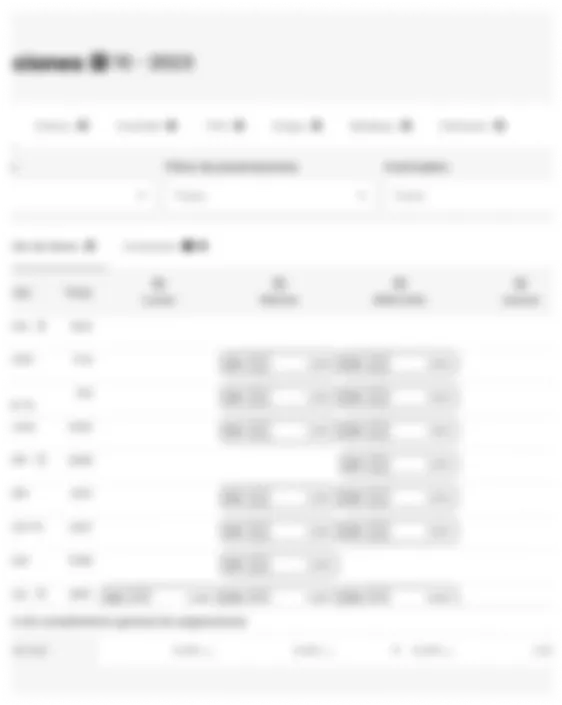
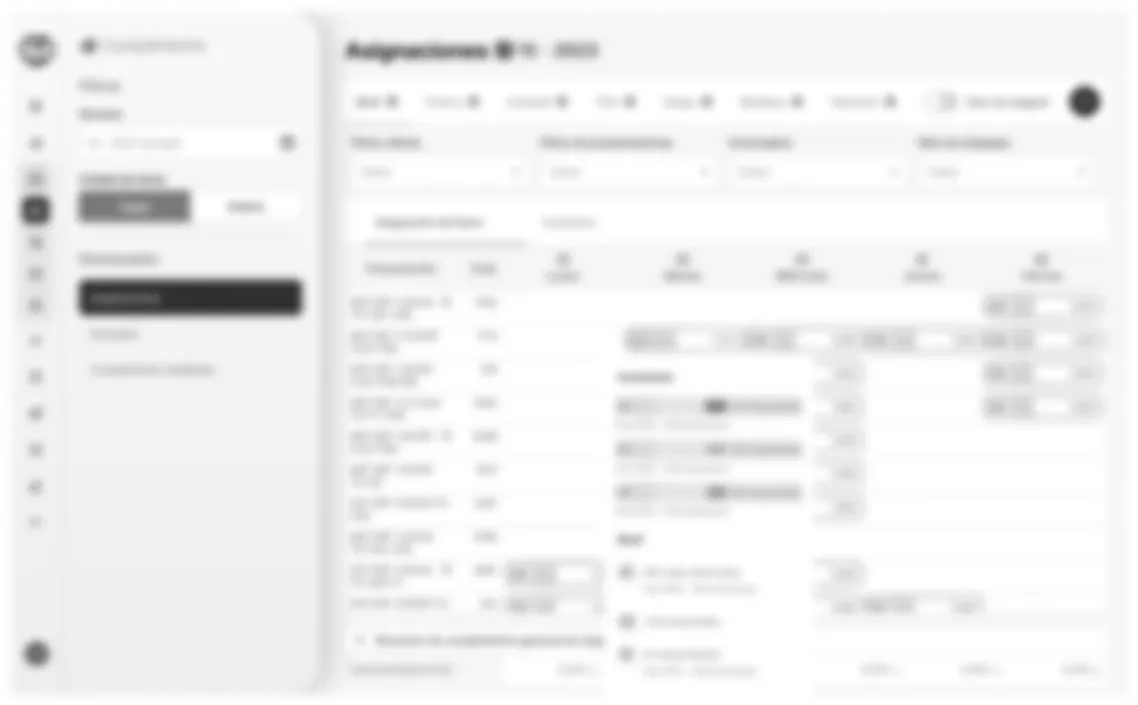
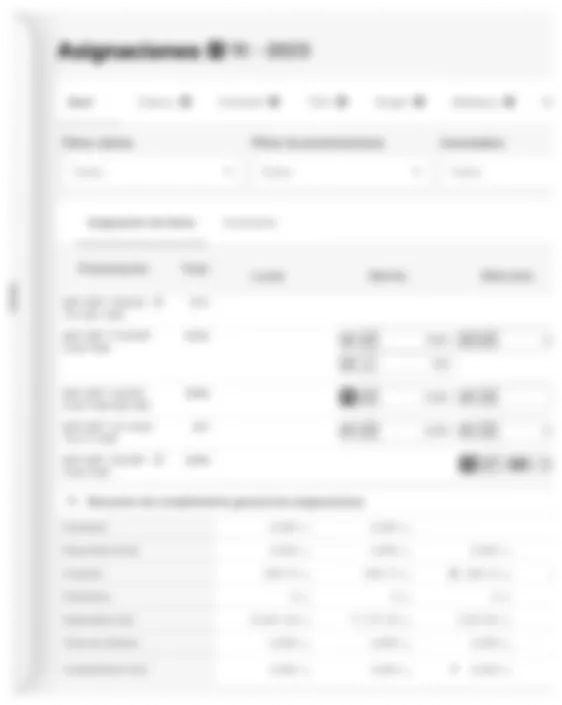
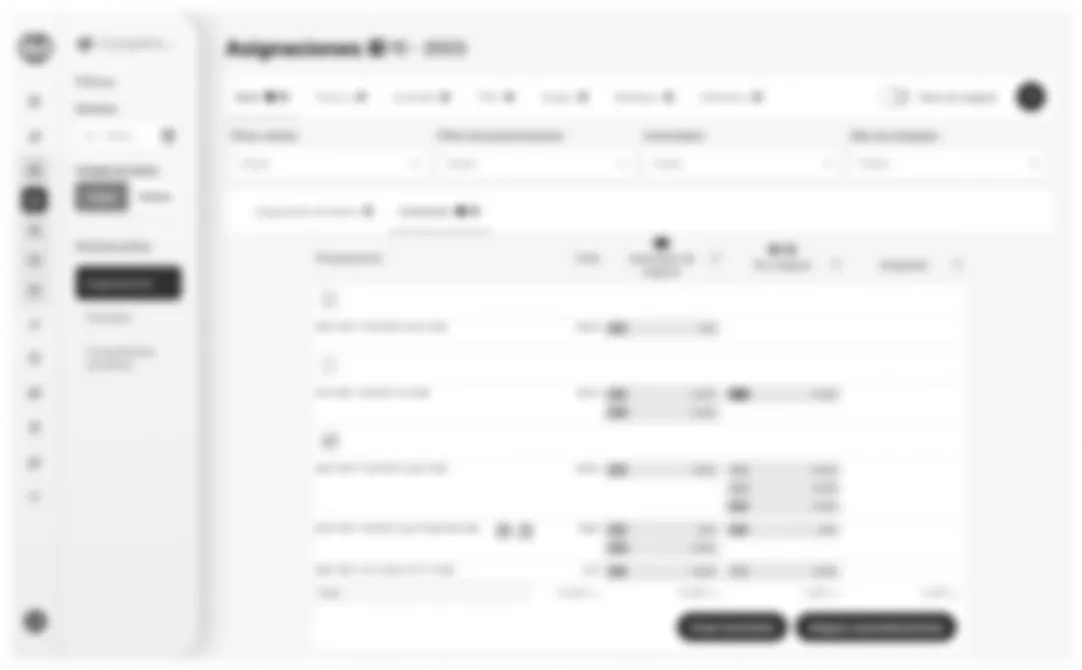
Greenhouse Selection
We evaluated and tested various iterations for assigning greenhouses, ultimately selecting a dropdown menu that prioritized products matching user requirements. Visual cues were implemented to highlight unassigned items, ensuring complete planning before proceeding.
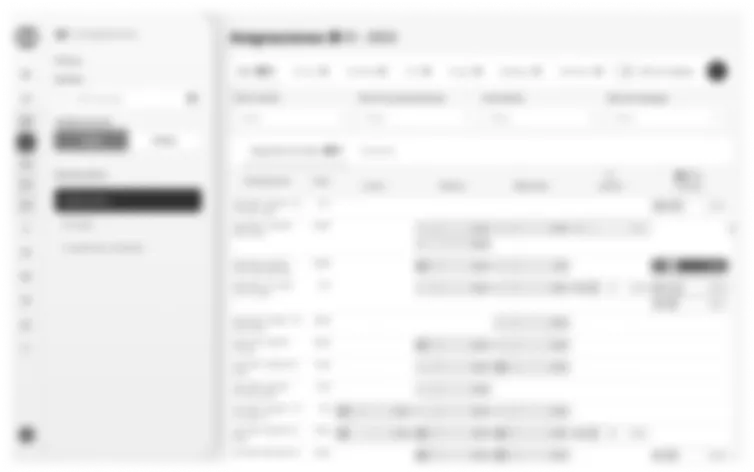

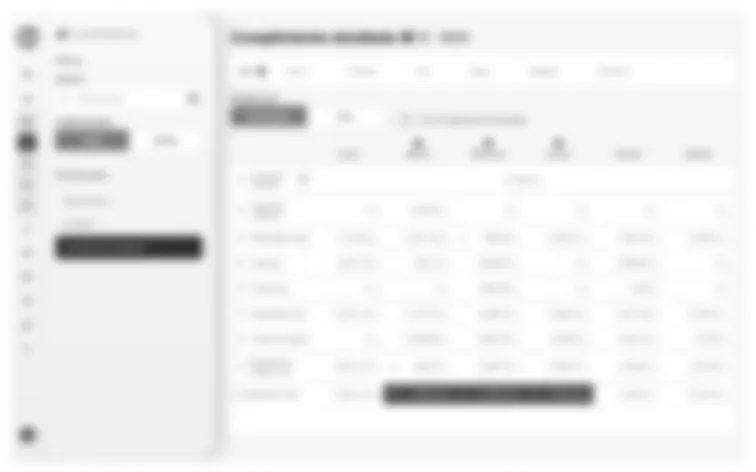
Cold Chamber Management
The cold chamber feature allows for managing packed items from previous weeks and identifying potential overpacking situations.
Packing Planning
We explored drag-and-drop functionalities for planning packing schedules, ensuring the interface facilitated clear communication of task requirements.
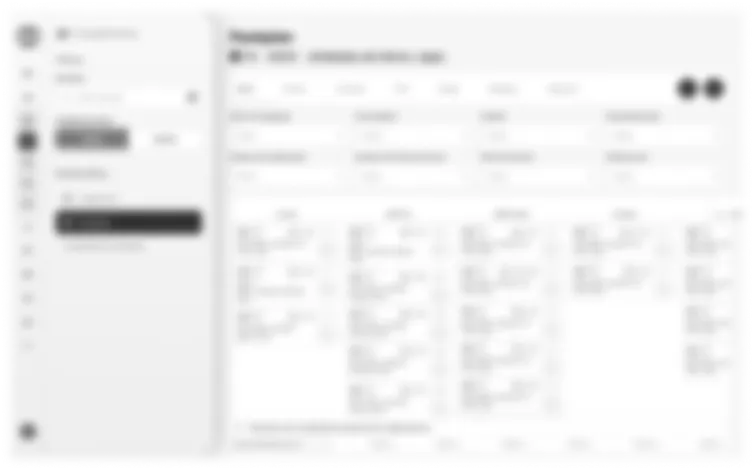
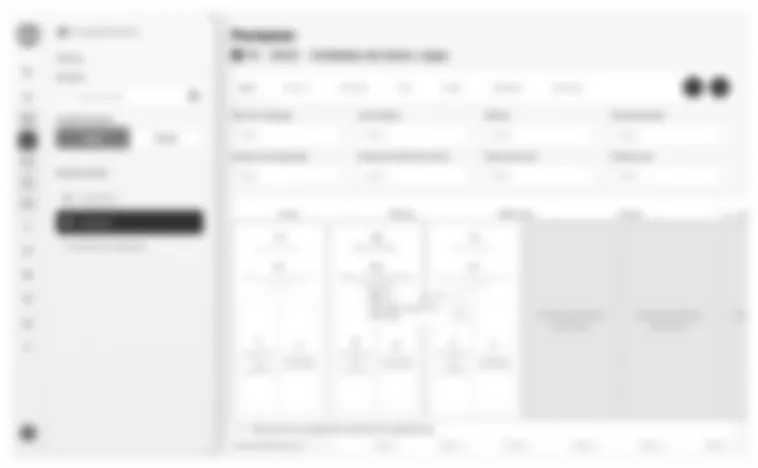
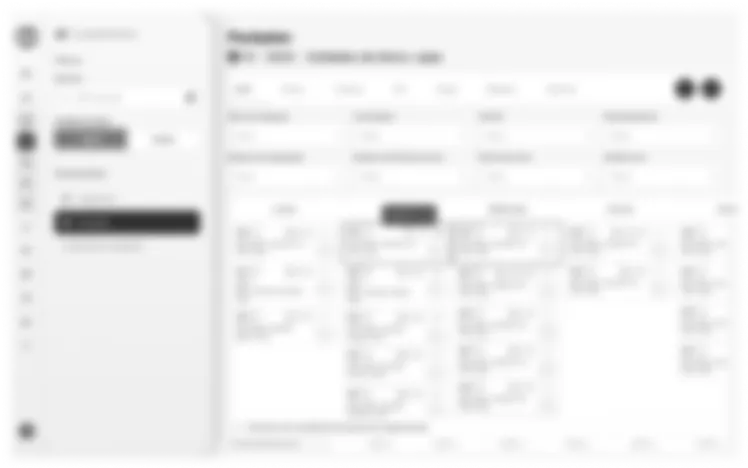
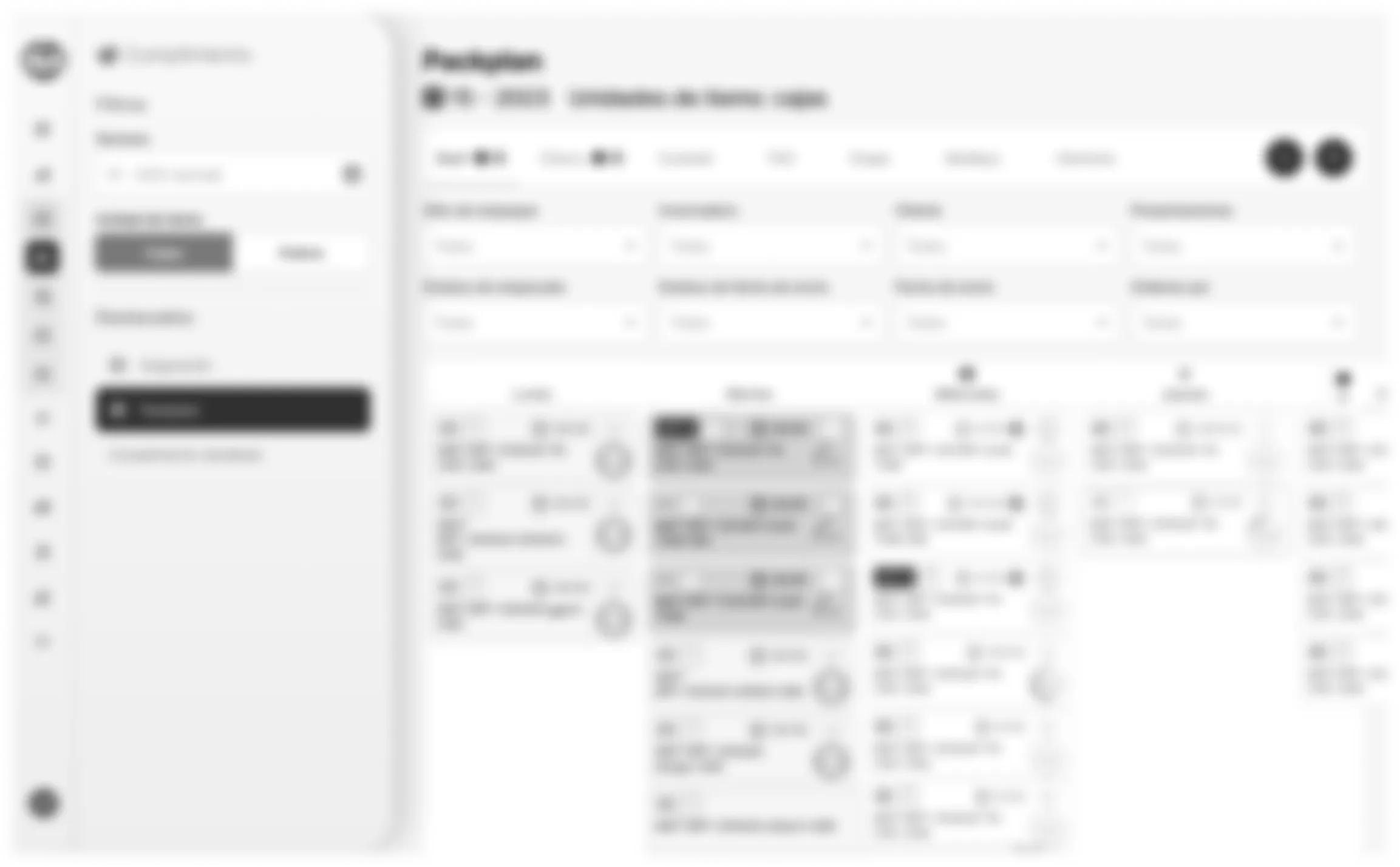
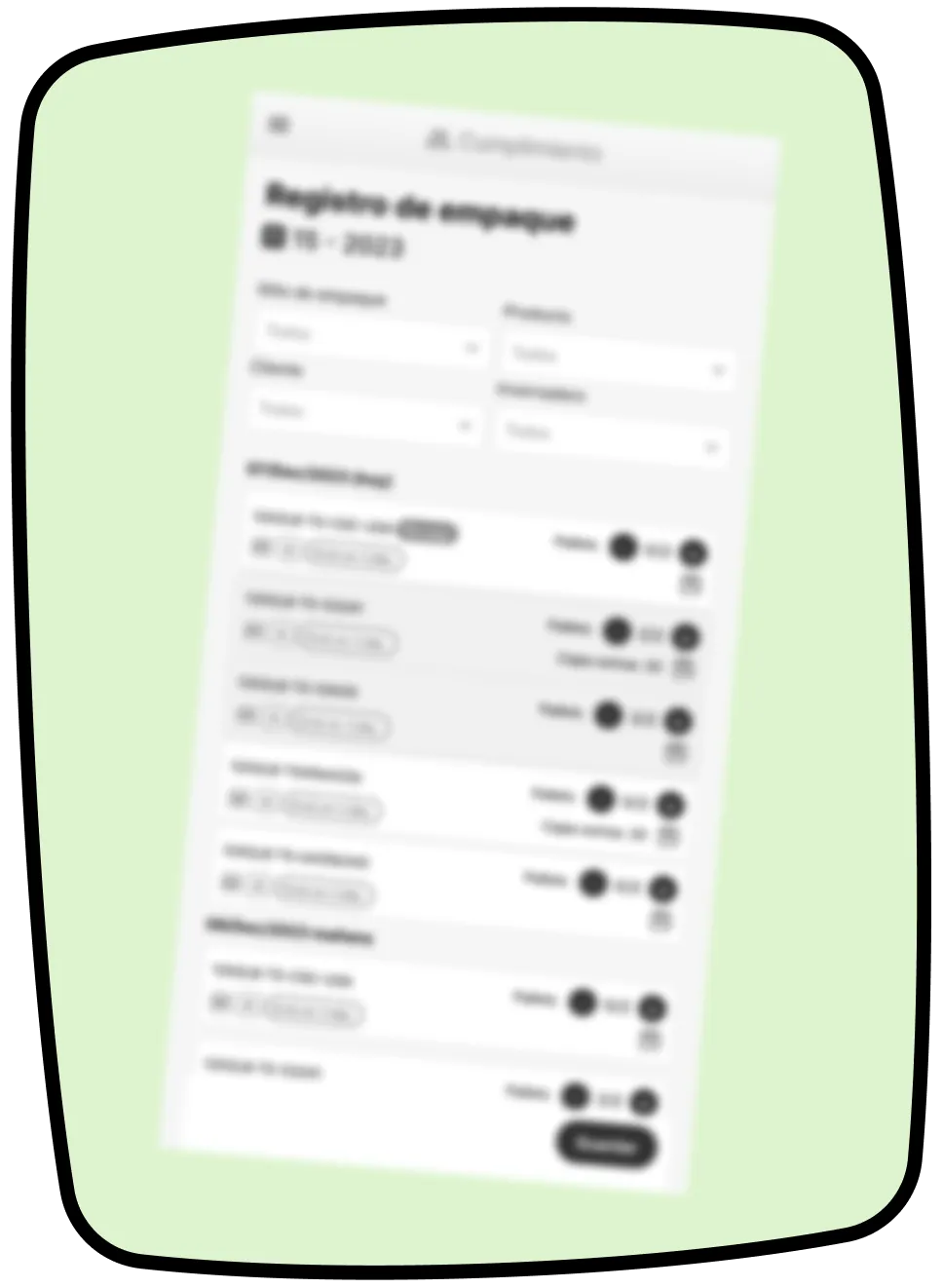
Packing Registration
We iterated on the design for real-time packing registration, ensuring the packing line leader had all the necessary information for efficient data entry.
Alerts and Notifications
We carefully designed alerts and notifications to provide users with the information they needed without overwhelming them. Overwhelmed users struggle to be productive.
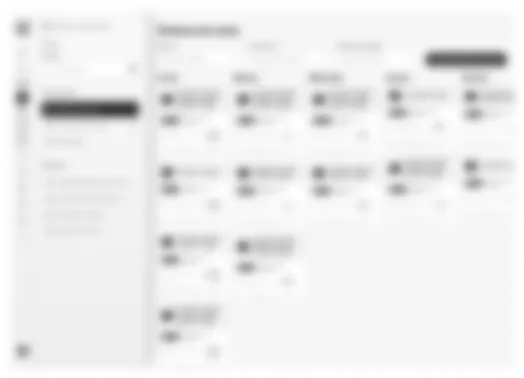
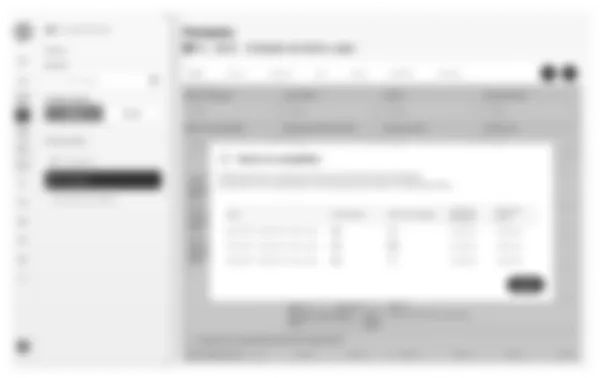
User-centered design saved the day! Initial assumptions missed the mark, but by prioritizing feedback and iterating, we designed a system that addressed real needs. This project solidified the importance of flexibility and a holistic approach, ensuring a streamlined solution for everyone involved.